Boltless vs Bolted VBRs: Which One's Right for Your Offshore Project?
We recently had a conversation with a long-time customer who asked, “What’s the real difference between your boltless VBRs and the traditional bolted ones we’ve been using?” It's a question we often hear, and after years of helping clients make the switch, we’ve seen firsthand the significant benefits that boltless clip VBRs provide.
Let's break down so many of our customers are making the switch—and how you can decide if it’s the right for your project.
1. Installation Time: A Simpler Process That Saves Hours
One common challenge we hear from customers is the time it takes to install traditional bolted VBRs. These systems often require bolts, washers, and metal components that take time and effort to manage.
Our boltless VBRs simplify the process by eliminating the need for bolts. As a result, installation is quicker and easier. In fact, many project managers have reported they cut installation time significantly by switching to boltless clips. Plus, installing our boltless VBRs usually requires just one person, compared to two for traditional systems. This saves both time and labor costs, which can have a big impact on your project budget.
2. Cost Efficiency: Saving More Than Just Installation Time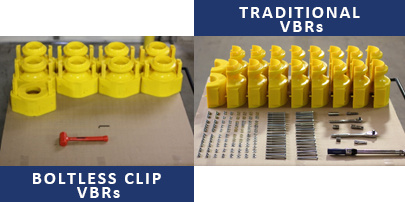
Budget is always a priority, and our boltless clip VBRs save money in more ways than one. A customer mentioned they no longer need to spend money on sourcing expensive bolts and hardware—which was a relief for both their budget and teams sanity!By eliminating extra parts, this simplifies the entire supply chain. It's not just about cutting costs during installation; it's about reducing ongoing expenses that come with maintaining and replacing hardware over time.
3. No Corrosion, Less Maintenance
A conversation with one of our customers drove home the value of our boltless VBRs. They were tired of dealing with corroded metal parts and the constant maintenance that came with them. After switching to our boltless VBRs, they were impressed by how well the clips held up with little to no upkeep required.
Since there are no metal components, there's no corrosion to worry about. This is one of the main reasons many of our customers choose boltless VBRs—they offer long-lasting performance with minimal maintenance.
4. Strength and Reliability: Real Feedback from Real Projects
We’ve received great feedback from customers who’ve put our boltless VBRs to the test. One project manager called them a game changer, saving their team hours during installation. Another shared how they felt more confident about their project's long term success thanks to the durability of our polyurethane clips.
Hearing these success stories is one of the most rewarding aspects of our work. When our products make our customers’ jobs easier and help their projects succeed, it reaffirms our commitment to providing real solutions that deliver lasting value in the field.
Want to Learn More?
If you're unsure which VBR option is best for your project, our team is here to help. We've guided many customers in finding the right solutions to meet their unique needs, and we'd be happy to do the same for you!
Contact us today to explore your options, or take a closer look at the specs in our VBR Catalog. Don't miss our cost savings calculator there - it's a quick way to see how much you can save with our boltless clip design.