Choosing the Right Material: Polyurethane vs. Silicone - What You Need to Know!
When it comes to selecting materials for your products, understanding the differences between silicone and polyurethane is crucial. Both materials are widely used in various applications, yet their distinct physical properties and environmental tolerances can greatly impact performance and durability
In this post, we'll dive deep into the unique characteristics of polyurethane and silicone, helping you make informed decisions that best suit your design requirements.
What You'll Learn:
- Material Properties: Discover how polyurethane and silicone compare in terms of flexibility, hardness, and temperature resistance.
- Applications Suitability: Learn which material is best for specific applications, from consumer goods to industrial components
- Cost Considerations: Understand the economic implications of using silicone versus polyurethane in your projects
What is Silicone?
Silicone, or polysiloxane, is a rubbery elastomeric material composed of carbon, hydrogen, oxygen, and silicon. Like polyurethane, most silicone types are thermosetting materials, taking on various shapes depending on viscosity and manufacturing process.
There are three main types of silicone: Liquid Silicone Rubber (LSR), High Consistency Rubber (HCR), or Room Temperature Vulcanizing (RTV). Each type has unique physical properties and molding techniques suitable for different design needs. Additionally, chemical additives can be incorporated in silicone during its raw, liquid state to achieve a range of properties, including tear strength, temperature, electrically conductive, and flame resistance. Silicone is available in hardness levels between 10 to 90 Shore A.
What is Polyurethane?
Polyurethane is formed through the chemical reaction between a polyol and diisocyanate. It can be engineered to be soft and flexible or hard and rigid. Thermoset polyurethanes, in particular, can be chemically engineered into solid or foam materials, offering a wide range of physical properties and surface finishes through a cast molding or Reaction Injection Molding (RIM) process.
Cast molding allows significant customization to meet specific design and performance requirements, while RIM combines the superior properties of thermoset polyurethanes with the adaptability of injection molding techniques. Polyurethane is available in three hardness scales: Shore A, D, and 00. Learn more about hardness measurement here.
Differences Between Silicone & Polyurethane
Despite their similar applications, silicone and polyurethane have key differences:
Silicone | Polyurethane |
Commonly injection, cast, or compression molded | Commonly cast or Reaction Injection Molded (RIM) |
Foam is often considered a specialty material, due to high costs & processing difficulties | Can be engineered into various solid and foam types |
Hardness levels typically range in Shore A scale | Hardness ranges across Shore A, D, 00 scales |
Withstands temperatures from -65°F up to 500°F | Withstands temperatures from -80°F up to 300°F |
High temp resistance but often low tensile strength, abrasion resistance, and durability | High abrasion resistance, tensile strength, & durability; properties can be customized |
Generally higher material costs, especially for foam | More economical for small & large production runs |
Which Material Should You Choose?
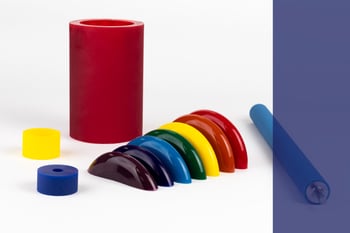
Both silicone and polyurethane can fit into a wide range of products and components, depending on application and performance requirements. Polyurethane often produces stronger, more robust products with diverse physical properties, making it suitable for applications in military & defense, medical devices, and paper & media handling to name a few.
Silicone often excel in applications requiring high temperature resistance, commonly found in consumer and medical products, such as baby goods, cooking supplies, and tubing or hoses. When evaluating your options, consider the key physical properties required for optimal performance.
If you need material assistance for your product design idea, complete our design tool, here, or download our Durethane datasheet below to explore the superior properties available.