What is Compression Molding?
Compression molding is one of many techniques related to the cast molding process. The only difference between the two is that compression molding requires compressive forces, usually in the form of a press, to achieve the desired net shape – Think of it like making the perfect waffle. A specific amount of liquid is poured into the center of an open bottom mold cavity, or in this case, a waffle iron. Before the mixture begins to solidify, a secondary mold is applied on top to compress the same shape and surface of the mold cavity. Eliminating this pressure from the process could alter the geometry and leave you with something completely different, like a flat pancake… How boring!
To learn more about compression molding and how it may be beneficial to your product design, continue reading below:
How Does Compression Molding Work?
While there are different techniques for compression molding, there are usually four main steps involved. For starters, specialized tooling is often needed to mimic the same geometry and dimensions as the engineered drawing. Typically, tooling may consist of a bottom mold and a top mold machined from aluminum or steel. However, hydraulic presses can also be integrated into the process depending on the overall design requirements and features. Once the tooling has been successfully developed, a specific level of raw materials is introduced into the bottom mold cavity. While many materials can be used in compression molding, such as thermoplastics, this manufacturing process is ideal for thermosets like polyurethanes. Afterward, the top mold with matching geometries is placed on top as the material begins to cure. A hydraulic press may be used at this time for additional pressure to prevent material from overflowing, creating a uniform part with minimal to no flash. The mold is kept tightly sealed for a specific period, enabling the material to cure fully into the final shape. Ultimately, the upper mold or hydraulic press is removed, and the final product is demolded. Depending on the tool design, compression molding can take on most complex shapes, patterns, and textures. Additional design features, such as inserts, can be molded-in or included as a secondary step.
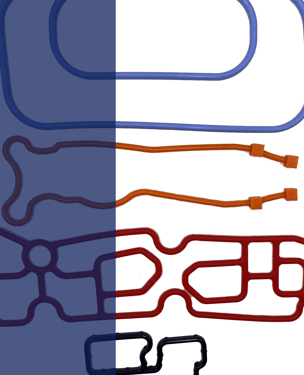
The Benefits of Compression Molding
- Compression molding can be used with a broad range of materials to achieve specific performance requirements. As a result, materials like thermoset polyurethanes are often considered for their superior properties, chemical resistance, and adaptability.
- Several compression molding techniques can be implemented to achieve a wide range of products with complex geometries or fine features. The compressive forces applied during this process enable the material to fill the entire mold cavity, leading to precise results.
- Compared to other processes, compression molding is often the most cost-effective and efficient method to produce small and large volumes. Unlike injection molding, this process does not require extensive equipment to regulate temperature or pressure, or high tooling costs.
Compression Molding in Product Design
Many designers rely on compression molding to manufacture a wide range of shapes, sizes, and forms. Compression molding, especially with thermoset polyurethanes, provides a great solution to obtain high-quality products and components for applications including industrial, medical devices, and packaging to name a few. Take the automotive industry as an example. There are many intricate parts with specific performance requirements that are essential in the making of automobiles. Parts, like specialty seals and gaskets to exterior panels, rely significantly on mold design and processing techniques for precise results. Without adequate tooling or compressive forces, parts are more susceptible to significant flash, sink marks, and overall inaccurate geometries. To avoid this, make sure to include a trusted manufacturing partner early in the design process to best inform your product design.
If you believe compression molding with thermoset polyurethanes may be the right process for your product design, complete our design tool, here, or download our material data sheets below to begin your custom product or component!