Polyurethane Rollers in Automation: The Ideal Solution for Factories & Warehouses
In today’s fast-paced automation environments, where reliability and efficiency are non-negotiable, every component plays a critical role. From high-speed conveyor belts to load-bearing rollers, automated systems in warehouses and factories demand parts that withstand constant wear, heavy loads, and rigorous operating conditions. For design engineers, selecting materials that extend component life and enhance performance is essential—and polyurethane is increasingly the preferred solution.
At MPC, our proprietary Durethane® solutions empower engineers to design components tailored for the most demanding automation applications. Known for its exceptional durability and adaptability, polyurethane consistently outperforms other materials in heavy-duty settings, making it a top choice for rollers, wheels, belts, and other key automation components.
Why Choose Polyurethane for Automation Systems?
1. Customizable for Every Application
Polyurethane’s chemical structure is highly customizable, allowing engineers to develop components precisely suited for specific automation requirements. MPC’s advanced materials can be engineered for enhanced impact resistance, abrasion resistance, and compression retention, ensuring maximum component longevity and reliable performance in even the harshest environments.
- Impact Resistance: Absorbs shocks and resists cracking under heavy loads, supporting consistent performance.
- Abrasion Resistance: Withstands wear from constant contact with other materials, prolonging part life.
- Compression Set: Maintains shape and functionality under stress, reducing maintenance downtime.
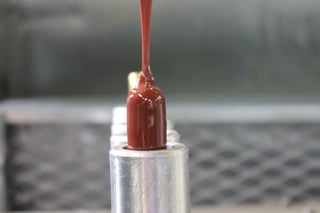
Polyurethane’s adaptability makes it ideal for moving quickly from prototype to final product. While some engineers may test materials like rubber, silicone, or plastic, polyurethane’s long-lasting resilience often emerges as the superior choice. Thermoset polyurethanes, in particular, deliver unmatched performance in high-demand applications. MPC’s expertise ensures rapid turnaround on high-performance prototypes, supporting project timelines without inflating costs.
3. Proven Reliability and Versatility
For years, polyurethane has delivered dependable performance in industrial settings, particularly for automation and material handling. Its resistance to temperature changes, chemicals, and moisture—combined with the ability to support both small and large production runs—makes polyurethane a reliable material for critical, high-volume automation parts.
Key Benefits of Thermoset Polyurethane Rollers
Key Benefit | Description |
Extended Roller Life & Reduced Downtime | High durability minimizes replacements, reducing system downtime and maintenance costs |
Noise & Vibration Reduction | Polyurethane's damping properties create a quieter, smoother operating environment, enhancing workplace safety |
Engineered for Specific Needs | Customizable in hardness, elasticity, and chemical resistance to meet diverse automation requirements. |
Energy Efficiency | Low rolling resistance lowers energy consumption, contributing to reduced operational costs for large systems |
Conclusion: Polyurethane as the Top Material Choice
When it comes to designing critical components for automation systems, selecting the right material is crucial to achieving high performance, durability, and cost savings. Polyurethane is an ideal choice for design automation engineers because it offers superior customization, a proven performance track record, and the ability to meet specific application demands across various industries.
By leveraging MPC’s expertise in materials engineering and manufacturing capabilities, engineers can achieve optimal solutions that meet both performance and quantity requirements. Whether you’re designing for harsh conditions, tight timelines, or high-volume production, polyurethane stands as the top material choice for your automation system’s components.